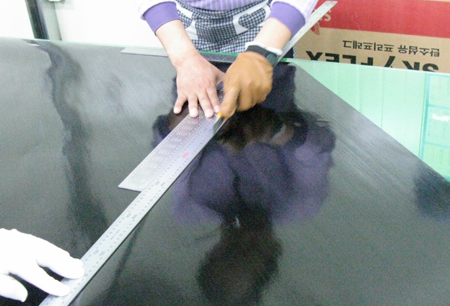 | 제작공정 1. 카본섬유 원단 재단 |
|
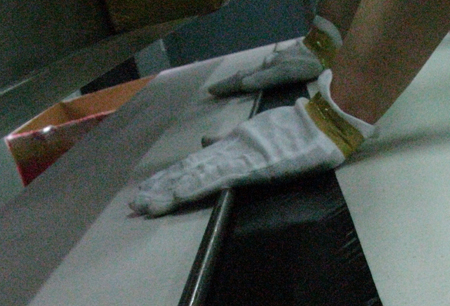 | 제작공정 2. 철 심봉에 원단 감은 뒤 테이핑 |
|
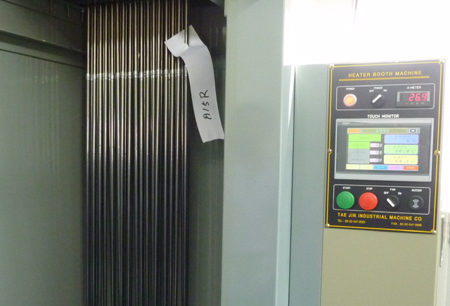 | 제작공정 3. 전기로에 넣고 가열 경화 |
|
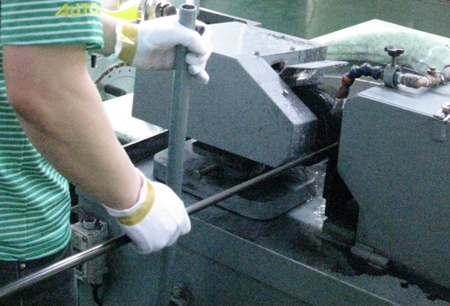 | 제작공정 4. 철심봉 빼낸 뒤 표면 연마 |
|
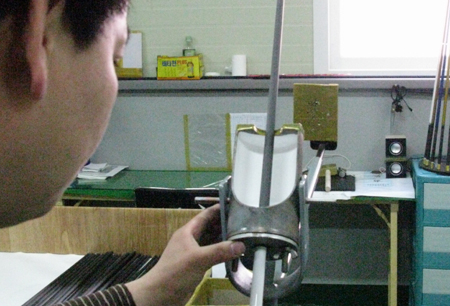 | 제작공정 5. 페인팅 및 24시간 자연경화 |
|
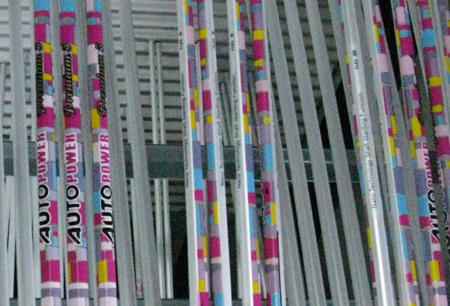 | 제작공정 6. 스티커 작업과 코팅으로 완성 |
|
가볍게 300야드를 날리는 한국프로골프(KPGA) 투어의 장타자 김대현은 드라이버로 타이어를 때리는 훈련을 통해 샷 거리를 늘렸다고 한다. 흔히 그라파이트라 부르는 카본 샤프트의 강한 경도와 탄성을 실감케 하는 얘기다.
카본 샤프트는 티타늄 헤드, 골프볼의 발달과 함께 샷 거리의 비약적인 증대를 가져온 주인공이다. 샤프트는 무엇으로 만들어지고 어떻게 그토록 잘 부러지지 않으며 탄성을 발휘하는 것일까. 궁금증 해결을 위해 최근 가동에 들어간 국산 샤프트 전문업체 ㈜미라이스포츠의 경남 함안 생산공장을 찾았다.
◇카본ㆍ수지 합성된 복합소재=카본 샤프트의 재료는 말 그대로 카본(탄소, 석탄ㆍ석유의 주성분)섬유다. 탄소섬유와 에폭시(플라스틱의 하나) 수지가 합성되면서 탄생하는 전혀 새로운 복합소재를 골프채의 샤프트로 쓰는 것이다. 탄소섬유는 가볍고 강도가 높아 복합재료 생산에 많이 이용되고 골프채는 물론 항공기와 로켓ㆍ자동차 제조 등 다양한 분야에 쓰이고 있다.
샤프트 생산 공정은 탄소섬유 원단을 약 10㎝ 폭으로 자르는 일로 시작된다. 공정을 요약하면 이렇다. ▲원단을 재단해 ▲수지를 바르고 ▲맨드릴(mandrel)이라 부르는 철 심봉(心棒)을 원단으로 감는다. ▲전기로에서 가열한 뒤 ▲맨드릴을 빼내고 ▲표면 연마와 페인팅 등 마무리 작업을 한다.
핵심 공정은 재단과 원단 감기, 가열 등이다. 재단에도 기술이 필요하다. 원단에는 한쪽 방향으로 결이 나 있는데 샤프트 설계에 맞게 결을 고려해야 한다. 결은 샤프트의 경도와 뒤틀림(토크ㆍtorque) 등 성능에 영향을 준다. 원단 감기는 핵심 공정 중에서도 꽃이다. 경력 20년의 신동재 공장장은 "맨드릴에 몇 장의 원단 조각을 어느 부분에 몇 바퀴 감느냐, 결의 엇갈리는 각도를 어떻게 하느냐에 따라 샤프트의 무게와 경도, 벤딩 포인트(힘을 받았을 때 가장 많이 휘어지는 지점) 위치, '손맛'까지 모든 게 완전히 달라진다"고 설명했다. 완벽한 원통을 만들어야 하기 때문에 감을 때 전체에 동일한 무게로 눌러주는 것도 중요하다.
원단을 감은 뒤 테이프로 감싼 상태로 전기로에 넣고 130℃의 온도로 2시간20분가량 가열하면 아세톤ㆍ에폭시 혼합 수지가 탄소섬유와 합성돼 파이프 형태로 경화된다. 마치 도자기를 구울 때처럼 가열 시간에 따른 온도 변화는 성질에 큰 영향을 주는 요소인 만큼 업체의 기밀사항이다.
◇멀리ㆍ똑바로ㆍ경쾌하게=박건율 미라이스포츠 대표는 "샤프트 개발의 키워드는 '탄성은 강하게, 뒤틀림은 적게, 감(손맛)은 경쾌하게'라고 할 수 있다"면서 "이 세 가지를 모두 갖춰야 골퍼들을 만족시킬 수 있다"고 강조했다.
샤프트 메이커들은 탄성으로 거리를 늘리고 뒤틀림을 잡아 방향성을 높이려는 연구에 몰두한다. 탄성에 치우치면 방향성이 떨어지고 방향을 잡으면 거리가 덜 나게 마련이다. 특히 최근에는 기술을 넘어 타구감을 중시하는 경향이 커지고 있다. 원단 재단과 감아주기, 가열 등의 과정에서 기술과 예술이 어우러져야 하는 이유다. 현대적인 기계화 설비가 된 이 공장이지만 직원들의 경력은 최소 10년부터 25년까지다.
박 대표는 "우리나라는 외국 골프 브랜드의 주문자상표부착생산(OEM)을 해왔기 때문에 경력과 기술을 갖춘 전문가가 꽤 많다"며 "좋은 손기술과 양질의 소재 사용으로 성능에서는 메이저 브랜드들과 어깨를 나란히 하고 있다"고 덧붙였다. 이 공장에서는 '오토파워' 'K' 시리즈 등 다양한 스펙의 드라이버ㆍ우드ㆍ하이브리드ㆍ아이언 샤프트 약 80종을 생산한다.